|
|
|
|
|
|
|
|
|
|
|
|
|
|
|
|
|
|
|
|
|
 |
|
|
|
|
|
|
Home
| Site index
|
|
|
|
|
|
|
|
Vibration
analysis is the ability to collect vibration data from machinery, interpret
the data to
establish the "health" or working condition
of that piece of equipment. |
|
|
|
|
|
|
|
|
|
|
What
is gained by the externally taken readings, is the ability to determine
location, and type of problems inside a piece of equipment,
without
removing it from service or disassembly.
Some problems that can be
detected by this method include: |
|
|
|
|
|
|
|
|
 |
|
|
|
|
|
|
-
Unbalance
or Misalignment.
-
Eccentricity
/ Bent shaft.
-
Weak structures.
-
Mechanical
Looseness.
-
Bad or
Worn Drive Belts and Drive.
-
Gear Problems.
-
Faulty
Bearings.
-
Electrical
Faults.
-
Rubbing.
-
Aerodynamic,
and Hydraulic Forces.
-
Resonance.
|
|
|
|
|
|
|
|
Data collection on turbo fan.
|
|
|
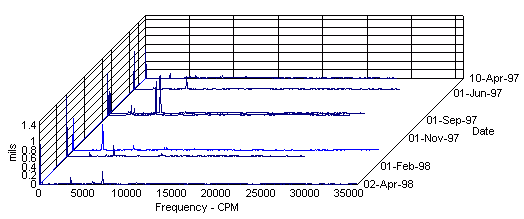 |
|
|
|
|
|
|
|
|
With
the use of database software, the deterioration of a piece of equipment
can be trended to determine when the unit must be removed from service,
before
it reaches catastrophic failure. |
|
|
|
|
|
|
|
|
|
|
|
|
|
|
|
|
|
The
money that is saved by planning maintenance to correspond with production
scheduling and
avoiding excess equipment damage and
repair costs after a severe failure is significant. |
|
|
|
|
|
|
|
|
|
|
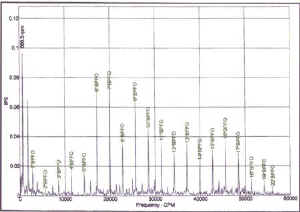 |
|
|
|
|
|
|
|
|
|
Many
production and process industries that implement preventative maintenance
programs, have seen
budgetary savings in the ten's
of thousands of dollars or more per year! |
|
|
|
|
|
|
|
|
|
|
|
|
Not
only can we find and predict bearing failures, we can also determine where
the problem is within the bearing. In this case the most wear is on the
outer race as indicated by the BPFO harmonics. |
|
|
|
|
|
|
|
|
Home
| Site index
|
|
|
|